Die Dichte-Masse-Kennzahl pro Volumeneinheit ist eine wichtige Messgröße in der komplexen Welt der Materialcharakterisierung und dient als Indikator für Qualitätssicherung, Einhaltung gesetzlicher Vorschriften und Prozessoptimierung in der Luft- und Raumfahrt, der Pharma- und Lebensmittelindustrie. Erfahrene Fachleute sind Experten in der Wahl der geeigneten Strategie und Instrumente für die direkte und indirekte Dichtemessung.
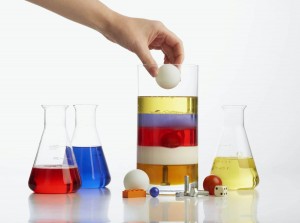
Direkte Dichtemessung meistern
Der Dichtewert lässt sich einfach ermitteln, indem man bei der direkten Dichtemessung die Masse einer Probe durch ihr Volumen teilt (Dichte = Masse/Volumen). Diese Methode ist für alle geeignet, die greifbare und praktische Prozesse bevorzugen. Das Volumen von Objekten wird durch geometrische Berechnungen bestimmt, bei denen das Eintauchen in einen Messzylinder das verdrängte Volumen angibt.
Dieser Ansatz eignet sich hervorragend zur Dichteberechnung von Metallkomponenten oder Kunststoffteilen in der Fertigungsindustrie. Der Reiz der direkten Messung liegt in ihrer Zugänglichkeit. So können Fachleute genaue Dichtewerte ermitteln, ohne große Mengen an Messobjekten zu benötigen. Unregelmäßige Formen erschweren jedoch geometrische Berechnungen, und winzige Proben stoßen an die Grenzen der Präzision herkömmlicher Geräte.
Raffinesse der indirekten Dichtemessung
Wie der Name schon sagt, werden Dichtewerte durch korrelierende Eigenschaften abgeleitet, wodurch direkte Massen- und Volumenmessungen vermieden werden. Die Vorteile der indirekten Dichtemessung liegen in ihrer Vielseitigkeit. Mit anderen Worten: Schwierige Probleme der Dichtemessung werden durch ultraschall- und strahlungsbasierte Ansätze überwunden.
Indirekte Dichtemessungen sind für die Echtzeitüberwachung wichtig, um die Effizienz zu steigern. Ihre Komplexität hat jedoch ihren Preis: Spezialgeräte wie Pyknometer oder Densitometer erfordern erhebliche Investitionen, und ihr Betrieb erfordert oft qualifizierte Techniker und eine sorgfältige Kalibrierung, um die Genauigkeit zu gewährleisten.
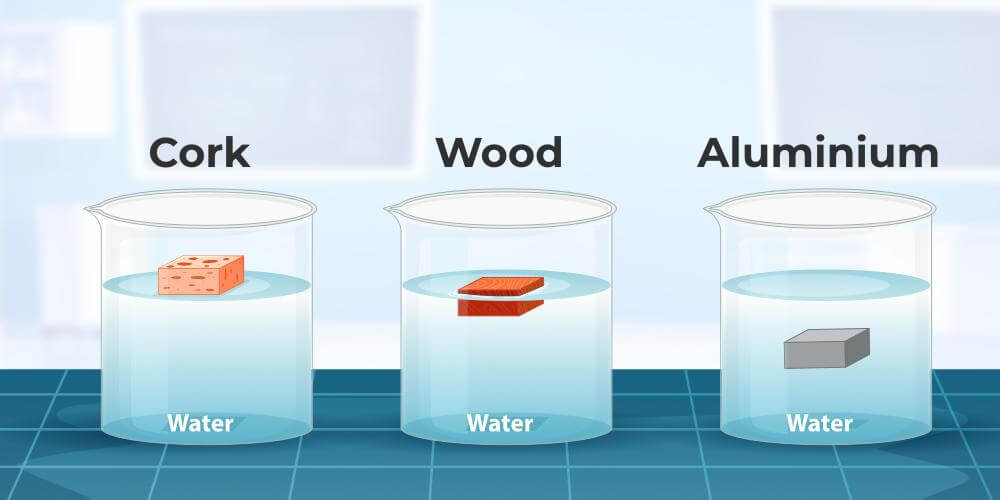
Die Kernunterschiede analysieren
Direkte Messungen basieren auf der physikalischen Quantifizierung von Masse und Volumen für taktile und intuitive Prozesse. Indirekte Messungen beruhen auf sekundären Phänomenen wie Auftrieb, Resonanz oder Strahlung. Um die Grenzen der Genauigkeit zu erweitern, ist ein tieferes Verständnis der Materialinteraktionen erforderlich.
Direkte Methoden basieren auf Messinstrumenten in Laboren, während indirekte Methoden fortschrittliche Prozesssensoren erfordern, wieStimmgabeldichtemessgeräteoderDensitometerauf bestimmte Anwendungen zugeschnitten, haben aber einen höheren Preis.
Bei gleichmäßigen Feststoffen oder Flüssigkeiten liefert die direkte Messung höchste Genauigkeit bei minimalem Aufwand. Indirekte Methoden überzeugen bei komplexen Proben – Pulvern, Schäumen oder Gasen –, allerdings hängt ihre Präzision von einer sorgfältigen Kalibrierung und der Fachkenntnis des Bedieners ab.
Direkte Messungen eignen sich für einfache Aufgaben wie Qualitätsprüfungen in der Lebensmittelproduktion oder pädagogische Experimente. Indirekte Messungen dominieren hingegen Spezialbereiche wie die Analyse pharmazeutischer Pulver oder die Dichtemessung von Erdöl, wo die Proben besonders komplex sind.
Strategische Auswahl für Ihren Betrieb
Treffen Sie eine strategische Entscheidung zwischen direkter und indirekter Messung entsprechend Ihren spezifischen Anwendungen, Budgets und betrieblichen Einschränkungen. Die Erschwinglichkeit und Einfachheit machen die direkte und indirekte Messung zu einer Selbstverständlichkeit für die Fertigung im Ausland, für kleine Fertigungsbetriebe oder für Bildungslabore.
Im Gegensatz dazu sind für Fachleute in der Pharma-, Luft- und Raumfahrt- oder Energiebranche, die mit Pulvern, Verbundwerkstoffen oder Flüssigkeiten arbeiten, indirekte Methoden unverzichtbar. Sprechen Sie mit unseren Ingenieuren und lassen Sie sich bei der Auswahl geeigneter Dichtemessgeräte unterstützen.
Beitragszeit: 08. Mai 2025